The working principle of the peanut shelling machine is actually to use the high-speed rotating rotor to keep flapping, and to destroy the peanut shell under the action of force through friction and collision with each other. After the peanut shells are broken, the peanuts fall out easily. Finally, the peanut shells are blown away by the fan and accumulated in a certain place, and the peanuts will stay. Some peanut shelling machines also have secondary shelling. When the first peeling is not clean, it will be left by the filter to facilitate the shelling again.
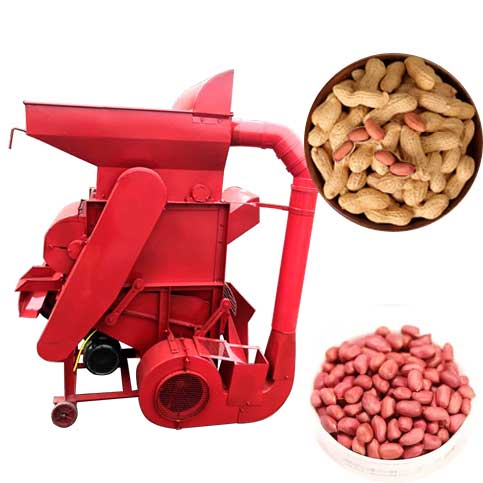
Before using it, we'd better conduct a comprehensive inspection of the peanut shelling machine, focusing on checking the rotating places such as the blades and gears, to ensure that they can operate normally, and properly apply some lubricating oil on the rotating bearings, and the operation will be smoother. , It also has a certain maintenance effect on the machine. Be sure to place the machine on a flat place when in use, so that it won't tip over while working. It is best to check the switch before use to avoid unnecessary accidents.
Preparation before using the peanut shelling machine:
1. Connect the 380V three-phase power supply before use, and then start the motor to see if the running direction is consistent with the direction of the indicated arrow. If it is inconsistent, switch any two connectors in the power supply to achieve the same direction as the indicated arrow.
2. After the test run, if all parts of the machine are running normally and there is no abnormal sound, the material can be put into production.
3. Before feeding into production, first sort the peanuts to be shelled, and separate peanuts of different varieties and sizes (for example, the fruit shapes of Dabaisha and Xiaobaisha are very different), and then determine the use of appropriate specifications. sieve, which can greatly improve the production efficiency and reduce the crushing rate.
4. The peanuts should not be too dry, otherwise they will be fragile. The moisture content should be kept around 9%. Otherwise, the breakage rate will increase. In this case, the water should be damped first, and the material can be put into production after waiting for 4 hours in winter (2 hours in spring).